Background
Imagine you are a nurse on the night shift. Most patients are asleep and stable. But some have oxygen deficiency, high blood pressure or fever. You're all alone and have to monitor hundreds of patients. Without technical aids.
This is exactly the challenge that machine measurement manufacturer Status Pro faced with its customers. Only we're not talking about human patients here, but machines or real estate, some of which are far apart doing their work. Most machines are fine most of the time. But it is, quite literally, vital to know early on whether a machine's condition is deteriorating. And not only when it is too late and the patient can no longer be saved.
Status Pro used its know-how in measurement technology to develop modern sensors that measure the "pulse beat" of the machines. However, measuring the values does not solve the challenge. The same applies here as with the nurse: She is not helped if only important vital parameters are measured. In addition, the data must always be made available to her reliably and in real time. With a large number of patients, it is important that she is made aware of the patients in critical condition and directly receives important additional information about the patient concerned, such as the illness and the attending doctor.
This in turn can be projected to the challenge of Status Pro and its clients: Successful monitoring requires:
1. reliable machine data;
2. fast and stable processing of the data;
3. intuitive information provision with a focus on critical cases;
4. relevant context for troubleshooting.
In addition, the necessary knowledge is often distributed across multiple stakeholders. For example, machine measurement engineers have the know-how on sensors, electrical machine builders on machines, and production line operators on production processes. This results in a high communication and coordination effort, especially when problems occur.
Complementary software for processing, visualizing and configuring sensor data was to address this complex challenge and increase added value for customers.
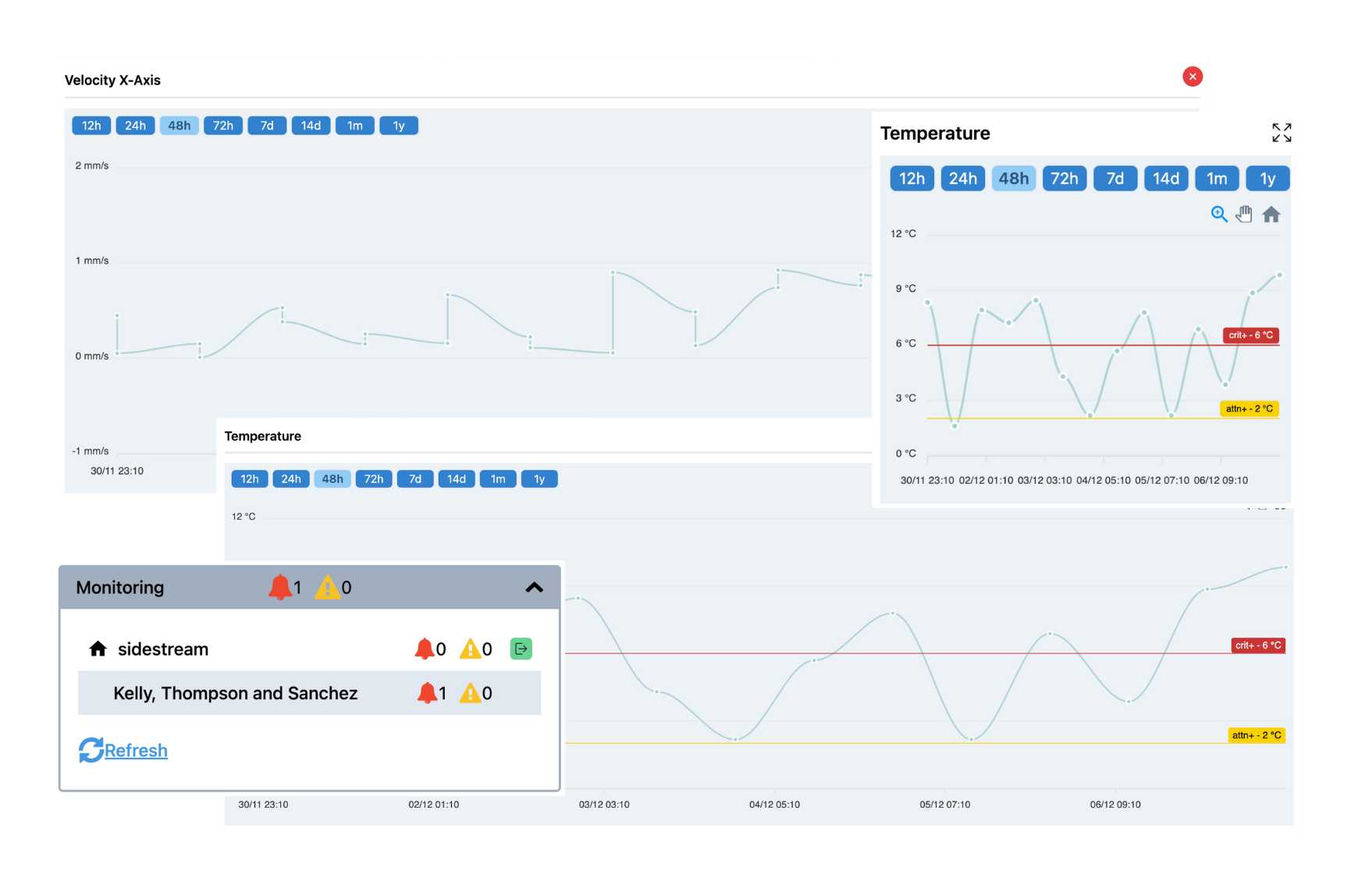
The solution approach
In the project, a solution for machine monitoring was developed. The focus is on software for processing, visualizing and configuring sensor data that is complementary to the sensors.
With the software, the various stakeholders can monitor their machine without having to be physically on-site. The machine builder can immediately see which machine is potentially in a critical state. He receives all the information relevant to indicating and rectifying the problem (e.g. location of the affected machine, contact persons, images and historical measurement data). He can then take the necessary steps to resolve the problem.
Key considerations include the following:
• Data security and sovereignty
Machine data is often sensitive data. Competitive advantages can be generated from the ownership and availability of the data. Accordingly, the developed software ensures that in the multi-tenant architecture, sensitive data is stored only in the customer's own database.
• One-stop-shop
The software is not intended to be just a simple monitoring interface, but the main point of contact for machine monitoring. Accordingly, the software was developed as a bidirectional application: In addition to providing and visualizing sensor data, the application also enables sensor configuration. This specification simplifies monitoring and maintenance. For example, alarm limits can be set individually, and measurement intervals can be defined.
• Intuitive and mobile use
Classic industrial software is often synonymous with cumbersome user interfaces and complicated, desktop-heavy programs. Status Pro's forward-thinking approach was to be underpinned by a modern and intuitive user interface. As in hospitals, monitoring is often done not only from the desktop, but from anywhere. Accordingly, the user interface and underlying infrastructure of the software is designed for mobile use from anywhere. At the same time, the implementation as a responsive web app has no restrictions on the security and scalability of the software. So, the best of both worlds.

Collaboration
As a specialist in the field of machine measurement technology, Status Pro has recognized the market potential for digital machine monitoring. The combination of Status Pro's experience in hardware programming and Sidestream's scalable and flexible software development ensures the perfect symbiosis for the project.
After Status Pro had already developed the hardware and validated the market need, Sidestream was brought on board to develop a robust and sustainable solution using modern software practices. After an initial concept phase, the project was developed over several months in two-week sprints. The subsequent development plan ensured that customers were able to see the software and provide feedback at an early stage:
- Development phase I is used to set up an infrastructure and the initial "cut-through" of data transmission from the sensor to the web application.
- In development phase II, the operation of the web application was improved and additional functions were added.
- In development phase III, the infrastructure and backend were brought up to live-gang level: the application has to scale to large volumes of sensor data and meet the customer's security standards.
This means that the software is ready for the market and will be operated and developed incrementally so that all customer needs can be covered step by step.
SPIoT for electrical machine builders
Technology Deep Dive
The entire software was developed with a dedicated backend and database per customer for a Kubernetes cluster. Sensor data is made available via an MQTT broker, read out and then routed to the correct customer stack. This infrastructure ensures that the requirements for usability, scaling, security and data sovereignty are met in equal measure.
Each dedicated company stack consists of the following components:
- PostgreSQL relational databases for managing all data: TimescaleDB plugin for processing large amounts of sensor data
- User management via gotrue: User data is stored in PostgreSQL DB
- VueJS web application