Hintergrund
Stell dir vor, du bist eine Krankenschwester in der Nachtschicht. Die meisten Patienten schlafen und sind stabil. Aber einige haben Sauerstoffmangel, Bluthochdruck oder Fieber. Du bist ganz alleine und musst Hunderte von Patienten überwachen. Ohne technische Hilfsmittel.
Genau vor dieser Herausforderung stand der Maschinenmesstechnik Hersteller Status Pro gemeinsam mit seinen Kunden. Nur handelt es sich hier nicht um menschliche Patienten, sondern um Maschinen oder Immobilien, die teilweise weit auseinander stehen und ihre Arbeit verrichten. Den meisten Maschinen geht es die meiste Zeit gut. Es ist aber, im wahrsten Sinne des Wortes, überlebenswichtig, frühzeitig zu wissen, ob sich der Zustand einer Maschine verschlechtert. Und nicht erst, wenn es zu spät ist und der Patient nicht mehr gerettet werden kann.
Status Pro nutzte dabei sein Know-how in der Messtechnik und entwickelte moderne Sensoren, die den „Pulsschlag“ der Maschinen messen. Mit der Messung der Werte ist die Herausforderung allerdings nicht gemeistert. Es gilt hier das gleiche wie bei der Krankenschwester: Ihr ist nicht geholfen, wenn lediglich wichtige Vitalparameter gemessen werden. Zusätzlich müssen ihr die Daten stets verlässlich und in Echtzeit zur Verfügung gestellt werden. Bei einer Vielzahl an Patienten ist es wichtig, dass sie auf die Patienten in kritischem Zustand aufmerksam gemacht wird und direkt wichtige Zusatzinformationen zum betroffenen Patienten, wie z. B. Erkrankung und den behandelnden Arzt, erhält.
Dies lässt sich wiederum auf die Herausforderung von Status Pro und seinen Kunden projizieren: Für ein erfolgreiches Monitoring braucht es
1. verlässliche Maschinendaten,
2. eine schnelle und stabile Verarbeitung der Daten,
3. eine intuitive Informationsbereitstellung mit Fokus auf kritische Fälle,
4. relevanten Kontext zur Problembehebung.
Zudem ist das nötige Wissen oftmals über mehrere Stakeholder verteilt. So verfügen die Maschinenmesstechniker beispielsweise über das Know-how zu Sensoren, die Elektromaschinenbauer zu den Maschinen und die Betreiber der Fertigungslinien zu den Produktionsabläufen. Das hat einen hohen Kommunikations- und Koordinationsaufwand zur Folge, insbesondere beim Eintritt von Problemen.
Durch eine komplementäre Software zur Verarbeitung, Visualisierung und Konfiguration der Sensordaten sollte diese komplexe Herausforderung angegangen und der Mehrwert für Kunden gesteigert werden.

Der Lösungsansatz
In dem Projekt wurde eine Lösung zur Maschinenüberwachung entwickelt. Im Fokus steht dabei eine zu den Sensoren komplementäre Software zur Verarbeitung, Visualisierung und Konfiguration der Sensordaten.
Mit der Software können die verschiedenen Stakeholder ihre Maschinen überwachen, ohne physisch vor Ort sein zu müssen. Der Maschinenbauer sieht dabei sofort, welche Maschine sich potenziell in einem kritischen Status befindet. Er erhält alle Informationen, die zur Indikation und Behebung des Problems relevant sind (z. B. Standort der betroffenen Maschine, Ansprechpartner, Bilder und historische Messdaten). Anschließend kann er die notwendigen Schritte einleiten, um das Problem zu beheben.
Dabei stehen unter anderem folgende Überlegungen im Zentrum der Entwicklung:
• Datensicherheit und -souveränität
Bei Maschinendaten handelt es sich oftmals um sensible Daten. Aus dem Besitz und der Verfügbarkeit der Daten lassen sich Wettbewerbsvorteile generieren. Entsprechend sorgt die entwickelte Software dafür, dass in der Multi-Tenant Architektur sensible Daten nur in der kundeneigenen Datenbank gespeichert werden.
• One-stop-shop
Die Software soll nicht nur ein einfaches Monitoring Interface sein, sondern die Haupt-Anlaufstelle für die Maschinenüberwachung. Entsprechend wurde die Software als bidirektionale Anwendung entwickelt: Neben der Bereitstellung und Visualisierung von Sensordaten ermöglicht die Anwendung auch die Konfiguration von Sensoren. Diese Spezifikation vereinfacht die Überwachung und Wartung. Beispielsweise können individuell Alarm Limits gesetzt und die Messintervalle definiert werden.
• Intuitive und mobile Nutzung
Klassische Industriesoftware ist oftmals Synonym für umständliche Benutzerinterfaces und komplizierte, desktop-lastige Programme. Das vorausdenkende Vorhaben von Status Pro sollte durch ein modernes und intuitives Benutzerinterface untermauert werden. Wie im Krankenhaus erfolgt auch hier die Überwachung oftmals nicht nur vom Schreibtisch, sondern von überall. Entsprechend sind das Benutzerinterface und die zugrundeliegende Infrastruktur der Software für mobile Nutzung von überall ausgelegt. Gleichzeitig hat die Umsetzung als responsive Web App keinerlei Einschränkungen auf Sicherheit und Skalierbarkeit der Software. Quasi das Beste aus beiden Welten.
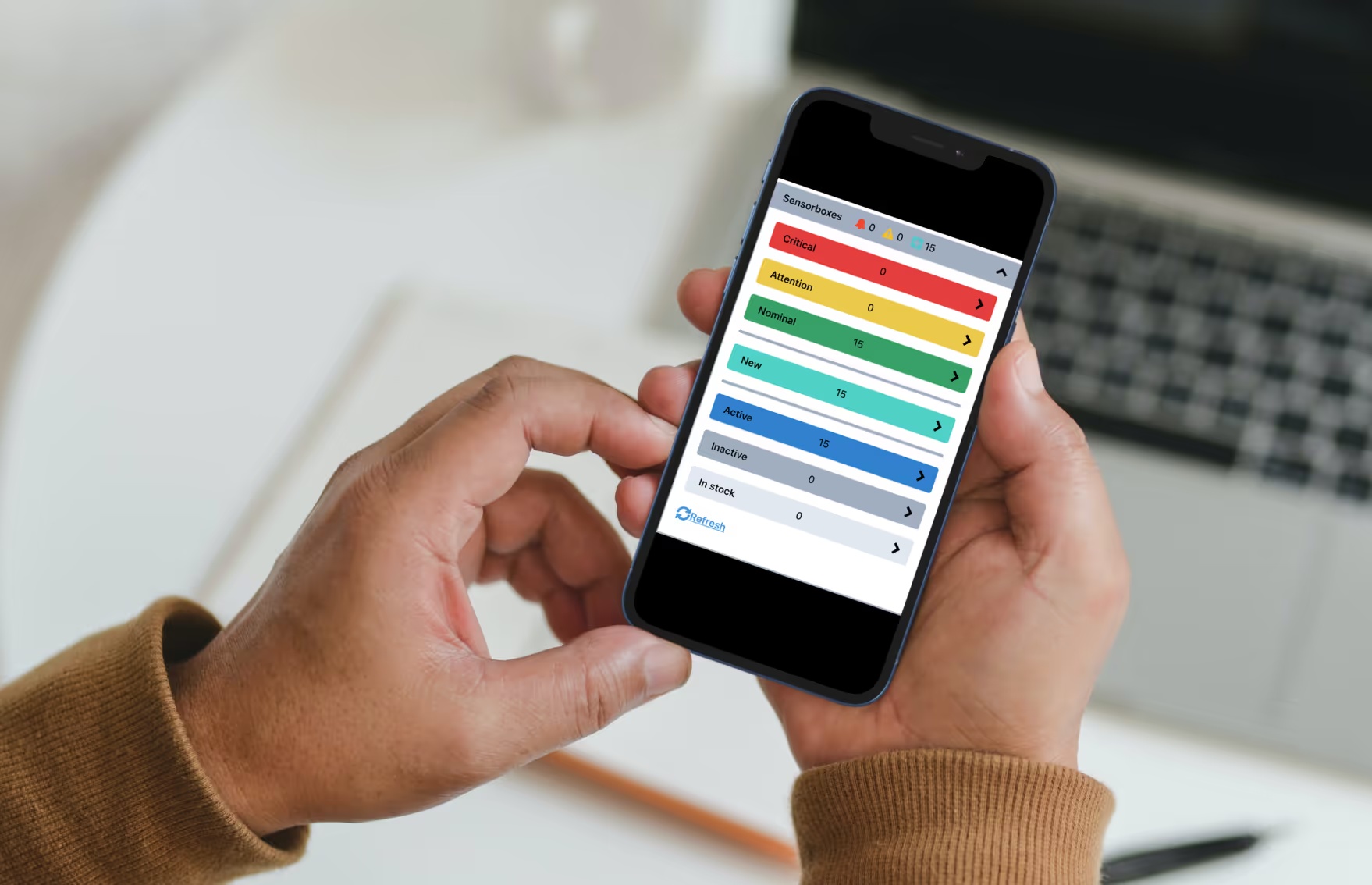
Die Zusammenarbeit
Als Spezialist im Bereich Maschinenmesstechnik hat Status Pro das Marktpotenzial für die digitale Maschinenüberwachung erkannt. Dabei sorgt die Kombination aus der Erfahrung in Hardware Programmierung von Status Pro und der skalierbaren und flexiblen Softwareentwicklung von Sidestream für die perfekte Symbiose für das Projekt.
Nachdem Status Pro bereits die Hardware entwickelt und den Marktbedarf validiert hatte, wurde Sidestream ins Boot geholt, um nach modernen Softwarepraktiken eine robuste und nachhaltige Lösung zu entwickeln. Nach einer initialen Konzeptionsphase wurde das Projekt über mehrere Monate in zweiwöchigen Sprints entwickelt. Dabei sorgte der folgende Entwicklungsplan dafür, dass die Kunden frühzeitig die Software sehen und feedbacken konnten:
- Die Entwicklungsphase I dient dem Aufbau einer Infrastruktur und dem initialen “Durchstich” der Datenübertragung von Sensor zur Webapplikation.
- In der Entwicklungsphase II wurden die Bedienung der Webapplikation verbessert und weitere Funktionen hinzugefügt.
- In der Entwicklungsphase III wurden Infrastruktur und Backend auf Live-Gang Level gebracht: So muss die Anwendung auf große Mengen von Sensordaten skalieren und die Sicherheitsstandards der Kunden erfüllen.
Damit wird eine Marktreife erreicht und die Software wird betrieben und inkrementell weiterentwickelt, sodass alle Bedürfnisse der Kunden nach und nach abgedeckt werden können.
SPIoT für Elektromaschinenbauer
Technologie Deep Dive
Die gesamte Software wurde mit dediziertem Backend und Datenbank pro Kunde für ein Kubernetes Cluster entwickelt. Über einen MQTT Broker werden Sensordaten zur Verfügung gestellt, ausgelesen und anschließend zum richtigen Kunden-Stack geroutet. Diese Infrastruktur sorgt dafür, dass die Anforderungen an Nutzbarkeit, Skalierung, Sicherheit und Datensouveränität gleichermaßen erfüllt werden.
Jeder dedizierte Firmen-Stack besteht dabei aus den folgenden Komponenten:
- PostgreSQL Relationale Datenbanken zur Verwaltung aller Daten: TimescaleDB Plugin zur Verarbeitung großer Mengen an Sensordaten
- User Management über gotrue: Nutzerdaten werden in PostgreSQL DB gespeichert
- VueJS Webanwendung